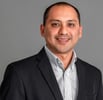
Oscar Salinas
Cabeza de Logística en Generac México
Actualmente, los problemas de logística se han aminorado debido a las tecnologías emergentes que optimizan los procesos, ya que estos evitan posibles inconvenientes y mejoran la capacidad de respuesta para evitar grandes perjuicios económicos.
Si quieres eludir tiempos de respuesta muy lentos, desinformación sobre el stock, ventas sin sustento físico de la mercancía o una terrible experiencia al cliente; entonces has llegado al post indicado.
Sigue leyendo y descubre cuáles son los 5 retos de logística más frecuentes que enfrentan las empresas y sus respectivas soluciones para que no te sucedan.
1. Manipulación incorrecta de la mercancía
Un aspecto clave para reducir los problemas de logística y aumentar la productividad es la correcta manipulación de las unidades de carga para conformar los pedidos.
Para ello, debemos asegurarnos que los trabajadores se estén bien capacitados, y que el almacén este equipado con elementos y equipos de manutención ideales con su respectivo mantenimiento al día.
No obstante, lo que garantiza el éxito del manejo de productos es la automatización de los sistemas de almacenamiento. A continuación, te mostraremos algunas soluciones de esta línea:
Pallet Shuttle
El Pallet Shuttle es un sistema de almacenamiento compacto en el que un vehículo con motor eléctrico se mueve sobre carriles por el interior de todos los canales de almacenaje. Estas máquinas pueden ser controladas fácilmente de manera remota con numerosas funciones avanzadas.
Es una tecnología que sustituye a las carretillas, lo cual, disminuye los tiempos de maniobra, aumentando el flujo de entradas y salidas de mercancía, mejorando la rentabilidad por la reducción de costos operativos y aumentando la productividad.
Asimismo, observarás una disminución en las incidencias y en costos de mantenimiento.
Asistencia al picking inteligente
Ya sea el picking por luz o voz, no solo agilizan el proceso, sino que hacen una preparación de pedidos más precisa. Esto incrementa la confiabilidad de los inventarios y los niveles de servicio a los usuarios y clientes de la compañía.
Sistema de gestión de almacenes
Los sistemas de gestión de almacenes representan una solución a la mayoría de los problemas de logística debido a su amplia variedad de funcionalidades que le aporta a nuestra industria flexibilidad, control, fluidez en los flujos informativos y de productos, entre otras ventajas.
Hoy en día existen en el mercado diversos sistemas ERP (Enterprise Resourcing Planning), tales como Oracle, SAP, LFS, Intelisis, entre otros. El principal papel de os sistemas de Gestión de Almacenes en la empresa es administrar y controlar las operaciones que se realizan en el recinto de forma diaria.
2. KPI de logística erróneos
Los Key Performance Indicators (KPI) o indicadores de rendimiento, por su traducción al español, son una herramienta fundamental dentro de cualquier industria para minimizar riesgos operativos.
Esto se logra debido a una recopilación, análisis y comparación de datos histórica de la empresa, donde podremos monitorear el rendimiento de una operativa para identificar posibilidades de mejora.
Entonces, cuando se hace referencia a los KPIS de inventario, se trata de aquellos indicadores de rendimiento que permiten tener un mantenimiento y control de todo lo relacionado al stock de la tienda, con el propósito de conocer a detalle la disponibilidad de productos.
Los indicadores logísticos pueden medir todas las operaciones realizadas en un almacén:
- Recepción de mercancías;
- almacenaje;
- preparación de pedidos;
- gestión de inventarios;
- expediciones;
- entregas;
- transporte y gestión de devoluciones; entre muchísimas otras.
Por lo tanto, si no aplicamos los KPIs correctos, será muy complicado —casi imposible— identificar la evolución negativa o positiva del proceso y no podremos actuar para remediarlas.
3. Inventario desactualizado
Tener el inventario desactualizado puede ser fatal, es uno de los problemas de logística de mayor peso debido a su implicancia en todo el proceso.
Un almacén que no tenga una actualización en tiempo real de la cantidad de mercancía que tiene disponible puede implicar graves consecuencias para una compañía, desde errores en la ubicación, hasta una probable rotura de stock.
A medida que las industrias van creciendo, deben incorporar un mayor número de referencias en su almacén, para esto, invertir en un sistema de gestión de almacenes es fundamental para conocer cada movimiento.
En efecto, este software tiene un flujo de información y procesos automatizados que genera una alta precisión y velocidad en el picking, mejorando los tiempos y evitando un desliz operativo que pueda significar grandes pérdidas económicas debido a una pésima experiencia al cliente que los cohíba de contratar nuevamente contigo.
4. Mal aprovechamiento de los espacios
Irónicamente, uno de los problemas de logística más frecuenta que debe enfrentarse una empresa es la falta de espacio de almacenaje.
Ante este inconveniente, que ocurre normalmente debido al incremento rotundo de la actividad, las organizaciones tienen la obligación de optimizar los espacios si no desean invertir —innecesariamente— un considerable gasto en suelo logístico.
Pero, ¿cómo podemos solucionar esta situación?
Para ello, hay que aprovechar la altura del almacén mediante el uso de estanterías firmes, de mayor altura o incluso, entreplantas y pasarelas. También podemos optar por soluciones más tecnológicas.
Un ejemplo son las estanterías metálicas de bases móviles para pallets. Este sistema se instala sobre bases móviles que se mueven lateralmente sobre carriles que están fijados en el piso.
El operario selecciona desde el control de mando remoto la base a la que necesita ingresar y las estanterías se abren automáticamente, dejando el pasillo de trabajo requerido para la función de carga y descarga entre las estanterías seleccionadas.
Esto optimiza la gestión del almacén y una consecuente reducción de los gastos de explotación de la empresa al promover una exitosa disposición y alta ocupación del espacio.
Una buena organización del almacén es un factor determinante para el éxito de la estrategia de ventas y, a largo plazo, puede ser una ventaja competitiva. El objetivo de esta gestión es optimizar tres aspectos principales:
- Uso del espacio.
- Uso de equipos.
- Gestión de recursos humanos para garantizar el máximo acceso a cada elemento y reducir los costes administrativos.
Un almacén eficaz está organizado de modo que cada operador puede encontrar rápidamente el artículo deseado y proceder a preparar el pedido de forma rápida y sin errores. Esto aumenta la satisfacción del cliente y optimiza la preparación de los pedidos y los tiempos de entrega.
5. Falta de organización de la mercancía
La falta de organización de los productos normalmente produce demoras y errores a la hora de buscar una determinada mercancía, complicando el cumplimiento de los tiempos de entrega pactados.
Si quieres prever estos problemas de logística, es preciso que elabores una eficiente estrategia de ubicación de productos que tenga como referencia las características, la rotación de mercancías, los sistemas de almacenaje disponibles y los desplazamientos de los operarios.
Los sistemas de gestión de almacenes promueven un control íntegro del stock mediante la sincronización de las órdenes de entrada y salida.
Una de sus funciones, por ejemplo, es automatizar el proceso de ubicación de las referencias del almacén a través de reglas y criterios preconfigurados.
Entre los criterios más importantes podemos señalar del slotting están: el índice de rotación de cada producto, fecha de caducidad o lote del artículo, flujos de mercancía en el almacén y las rutas de picking óptimas
Para finalizar, es indispensable que, para evitar problemas de logística, todas las industrias deban apoyarse en innovaciones tecnológicas para: identificar y atacar rápidamente los problemas, optimizar sus procesos y mejorar sus tiempos de respuesta de cara al cliente. Estos factores mejoran su rentabilidad y competitividad en el mercado.
¿Qué te pareció el post? Escríbenos en la casilla de comentarios tus impresiones. ¡Estaremos encantados de contestarte!